Proving the strength of formed tubes using mechanical bend tests
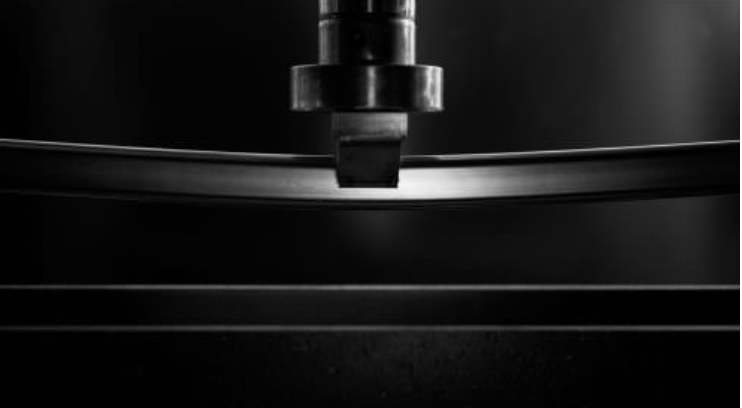
Stainless steel tubes: impressive ductility that provides strength and formability
Most of the tubing that we manufacture at Timeless Tube is formed from stainless steel for several reasons; it is strong, pliable and corrosion-resistant, and allows for a variety of beautiful finishes. It comes out top of any life-cycle cost analysis when compared with other materials, which makes it a sustainable choice.
Stainless steels fare well in compression and axial loading tests due to their impressive ductility, yet they are more complex than carbon steels. Factors such as the grade of the stainless steel and the manufacturing processes used prior to testing (such as cold-forming) all affect the form of the stress-strain curve observed in tests.
Evidence from mechanical bending/axial load tests carried out in controlled conditions combined with years of recorded knowledge from our workshop allow us to confidently predict which profiles will be structurally sound prior to a new size or shape being made.
This feature explores two of these mechanical bend tests, as well as the typical radius bend calculations we use to ascertain what ‘bend radii’ shaped tubes will withstand before buckling when further bending is required during fabrication.
Mechanical deflection tests for Timeless Tube’s shaped profiles
Timeless have proven the strength of our uniquely shaped tube profiles by testing how far 1m-long stainless steel 316/L lengths deflect when a downward force of 400kg is applied to the midpoint of the tube over a contact area of 50mm against the major axis of the tube.
This independent deflection testing assessed the effects of an axial load force upon each profile, using round tube as a control. (We tested axial load force as it is arguably the most common force applied to our tubes, in applications such as handrail, door handles and railway luggage racks). The various stress strain curves for each profile showed different points of deformation in response to the compressive load.
These carefully controlled experiments show that our unique profile shapes outperformed the standard round tube from which they are formed, offering improved strength and integrity. In fact, flat-sided oval and radiused square tube (flush) were as much as 54% stronger in than round tube in these deflection tests.
Find out more about these independent deflection tests.
Three-point bend tests on oval hollow section to justify its use in structural engineering applications
Professor Leroy Gardner from Imperial College London, alongside colleagues, carried out extensive tests on stainless steel oval hollow section using some large oval tube sizes, such as our 86x58x3mm – all with an aspect ratio of approximately 1.5. Gardner et al’s findings have helped make a case for including oval hollow section as a viable structural material to the Design Manual for Structural Stainless Steel.
In the 2009 paper ‘Flexural behaviour of stainless steel oval hollow sections’ by M. Theofanous, T. M. Chan and L.Gardner, three sizes of Timeless's cold-rolled, seam-welded oval tubing – 121x76x2mm, 121×76×3mm and 86×58×3mm – were used in in-plane three-point bending tests to ‘encompass a variety of section slenderness values and cover a range of structural responses’. The tests included one major and one minor axis bending test for each tube size.

The results have helped to change the possibilities for structural engineers as they have proved that oval hollow section can be safely adopted according to the same codified slenderness limits for stainless steel circular hollow section in conjunction with proposed equivalent diameters. The controlled experiments highlighted the effect of aspect ratio, cross-section slenderness and moment gradient on strength and deformation capacity. Combined with existing tests and FE testing, the results make for compelling reading.

See drawing 5.2 in the Design Manual for Structural Stainless Steel for the calculations that can be used by structural engineers to safely determine which oval hollow sections can be used in structural applications.
Radius bending for tube applications
As tube fabricators we are often asked to bend tube for varied applications – from boat pulpit rails to the rim guard that runs around large movie-set fans. Sometimes the requested bends can be achieved, and sometimes they are too tight. (When the bends requested are deemed to be too tight, our fabrication team can often find other ways of joining the tube).
When an oval tube needs bending, we use calculations from both mathematical models and our own empirical data to work out whether the radius of that bend will be possible, or if it is too tight. If the angle of the bend is too tight it will cause the stainless steel to go beyond its elastic limits, leading to wrinkling/necking or shearing.
Bending the minor axis is always easier than bending the major axis. You will often hear this described as bending ‘the hard way’ and bending ‘the easy way’ within the tube and pipe industry.
We use different methods for bending tubes depending upon the type of bend needed; a triple roller machine for sweeping curves, and fixed radius bending for tighter bends. Each bending tool that we have access to – made specifically for each size of profile – has its own bending capabilities. As a guide, a tube that needs to be bent on either the A-plane or B-plane using the fixed radius bending machine is likely to need a minimum centreline radius of 2.75 times the dimension of the axis. But the minimum centreline radius will vary depending upon the size and shape of the profile.
Experimenting with the tube’s wall thickness is also important when it comes to achieving the optimal bend. Increased tube wall thickness requires more force to achieve the desired bend but it means the tubing is less susceptible to collapse than a tube with a thinner wall thickness.

We experiment with new profiles to test their bending capacities, such as the relative newcomer, radiused rectangle. The rectangular profile photographed, measuring 58x34x1.5mm, was put through a triple roller machine to see how far we could bend it before necking occurred.
In reality, even without consulting any centreline radius bend charts, our highly experienced fabricators can very quickly tell from engineering drawings if the bends look as though they will be viable. If you have bending requirements speak to our team to discuss what is possible for your application.
More stories
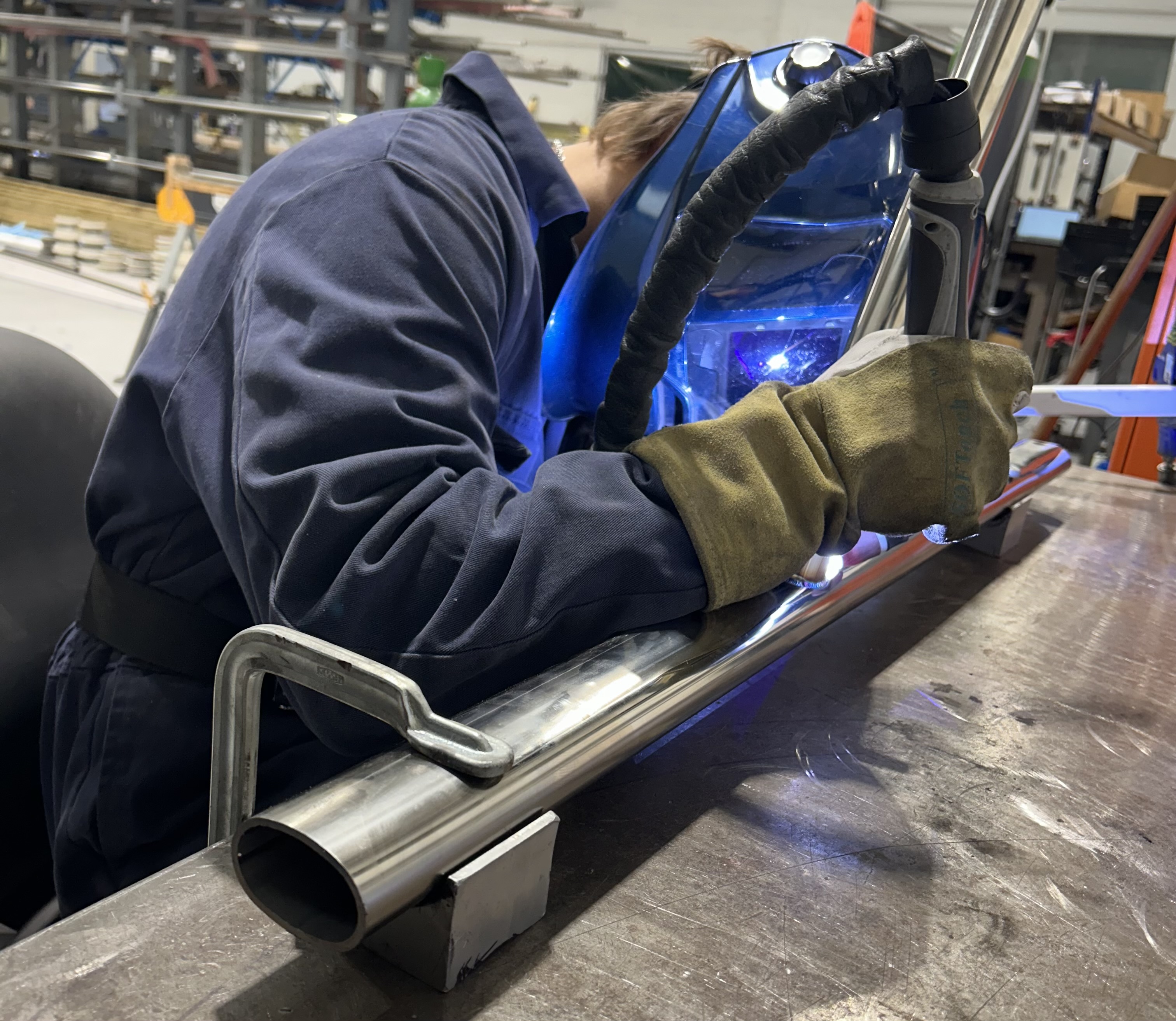
Exhibitors Timeless Tube engineer tube-based showcase for Southern Manufacturing and Electronics trade fair
Visitors to leading trade show for engineers and manufacturers to experience a showcase of innovative tube designs
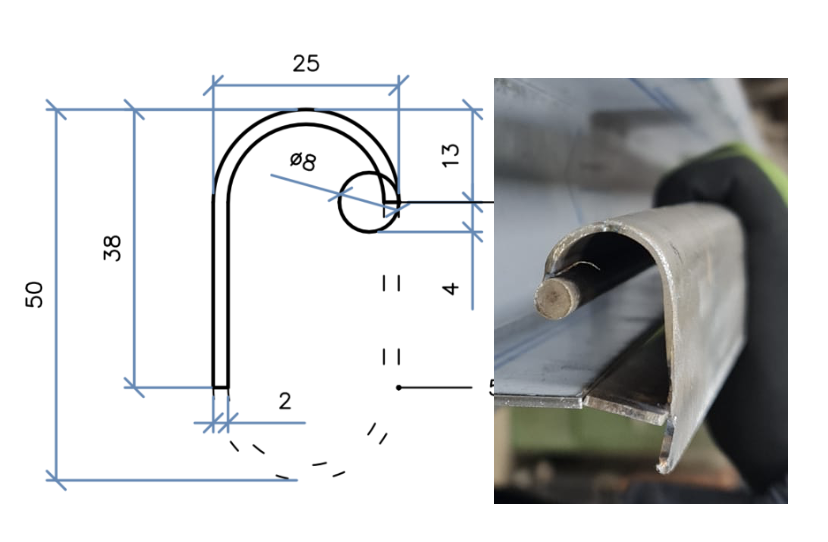
Cut Flat-sided Oval Tube Features in Stunning Recessed Handrail Project
Achieving unique designs often requires embracing trial and error. Timeless had the pleasure of working with pioneering UK-based bespoke steel fabricators Metcalfe on a one-of-a-kind recessed handrail
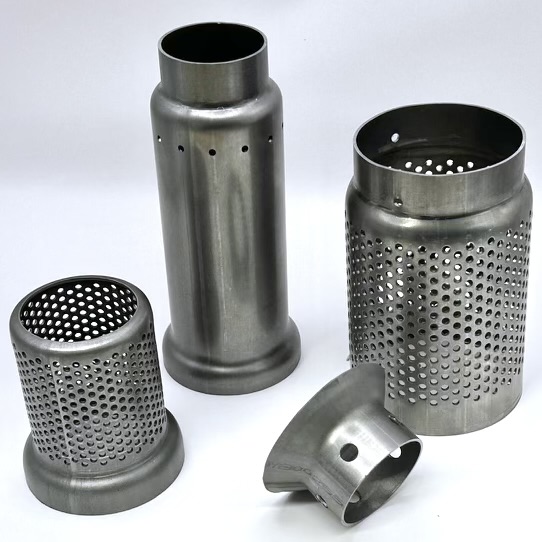
Adjustable tube expansion and reduction at Timeless Tube: a cost-effective, flexible service
We’re excited to announce that we have invested in new machinery that allows us to expand and reduce the ends for tube components.