How to choose the right weld seam for your tubing
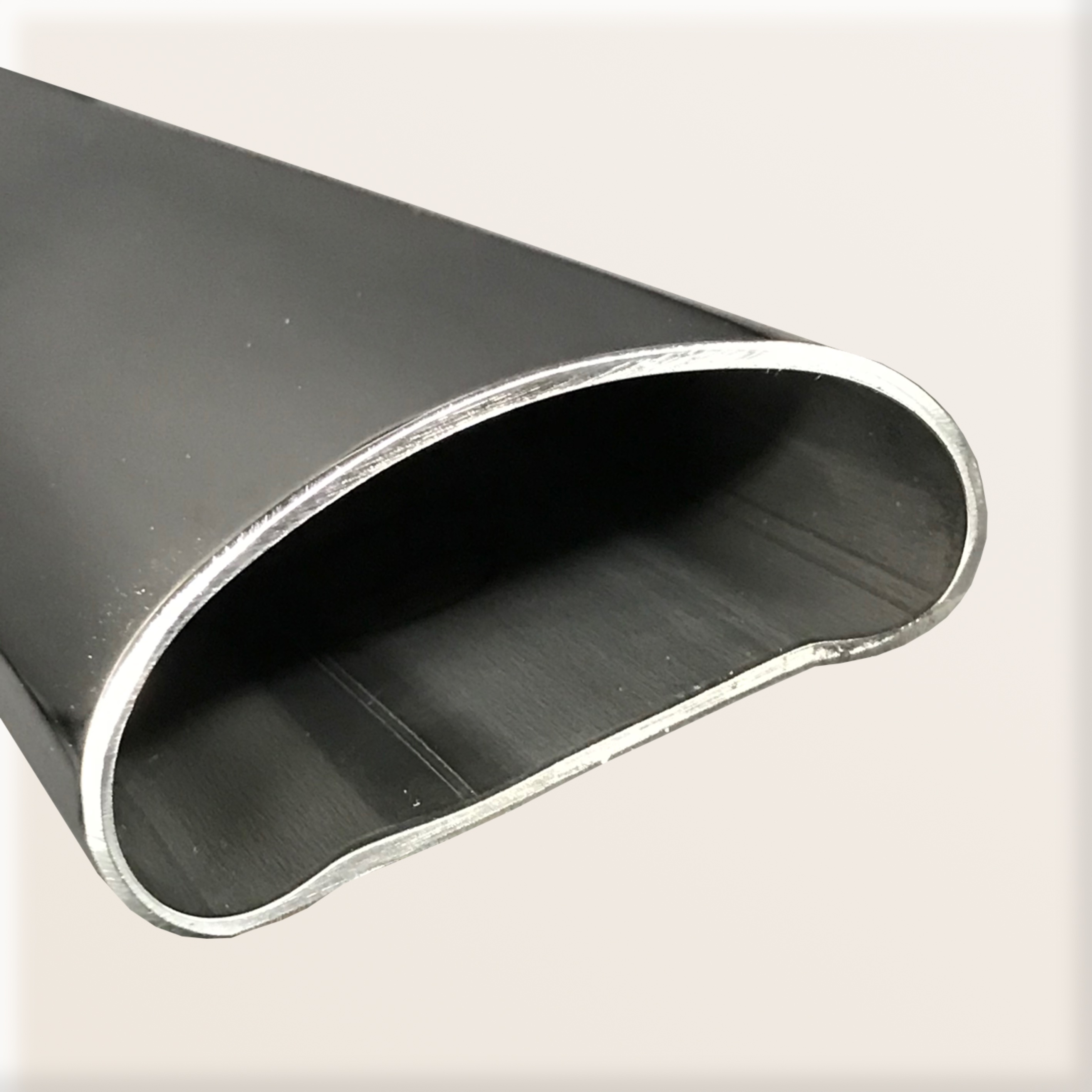
At Timeless we shape our metal tube from off-the-shelf round tube. But the round tube itself has to be made first. How that tube has been welded together at the seam makes a difference to the quality of our tubing, and therefore the quality of your application. So it is important to choose it wisely.
There are a few different ways that round stainless steel (inox) tube can be welded together during its production process.
High frequency welded tube – best avoided!
The cheapest way to weld round tube together at its seam is high frequency welding. This method allows for a manufacturer to create lengths and lengths of this tube within minutes (well, 100 metres per minute to be more precise). Heat is passed quickly all across the entirety of the tube as it speeds through the machine. The problem with this is that the heat may not then penetrate as deeply into the wall thickness of the tube as it needs to. If the heating is too superficial, the tube may not have truly bonded properly at its seam. If that tube is then bent or shaped during further fabrication, it may split. We have seen this happen during shaping when a client specified that we use high-frequency welded tube; we would not use this type of tubing again. It may be cheaper but the quality is inferior.
Laser-welded tube – a Timeless favourite
This is our preferred tubing. Laser-welding round tube at its seam directs the heat onto the precise area that needs welding, reducing the heat-affected zone (HAZ). This accurate isolation of the heat allows it to penetrate deep enough to allow for proper bonding. This results in great quality tubing. Less heat across the tube means less combustion activity – the alloying elements do not separate in the same way as they would in high frequency welding (which affects the whole tube). This means the tube retains the same characteristics of the parent material, since only a small area has been affected by the heat.
It takes longer to make this than high-frequency tube (about 10 / 15 metres per minute). But it is quicker to form than TIG welding, so less expensive. Unlike TIG welding, it doesn’t require a postweld ‘anneal’, which also keeps the cost down.
TIG-welded tube – strong but expensive
This conventional production process is commonly known as tungsten inert gas (TIG), but sometimes referred to as gas tungsten arc welding (GTAW). Filler rods are melted and added at the seam to join the metal. This is followed by heat-treating to anneal the weld seam. TIG welding produces really high-quality results, but it is a more laborious process so it is more expensive to buy. Pharmaceutical and aerospace might prefer this type of tubing.
Seamless tubing
This is the most expensive type of round tubing as it takes longer to make. It has no welded seam. When we form tube from cupronickel, aluminium and brass – essentially all non-stainless steel metals – the round tubes are seamless. To make it you need a mechanism to force the hole into the billet (rotary piercing and rolling is the most common way to make it).
We don’t often require seamless stainless steel tubing for the applications we make at Timeless, although we have used this before for some laboratory equipment through which fluid passed under pressure. It is great for critical applications such as this.
If you’re in any doubt what tubing to specify, please just talk to our team and we will be happy to chat about your application to select the most appropriate type for you.
Timeless Tube are extremely particular about the quality of the tube that we use when forming tubes. We only source materials from premium suppliers. Find out more about the metals we form from.
More stories
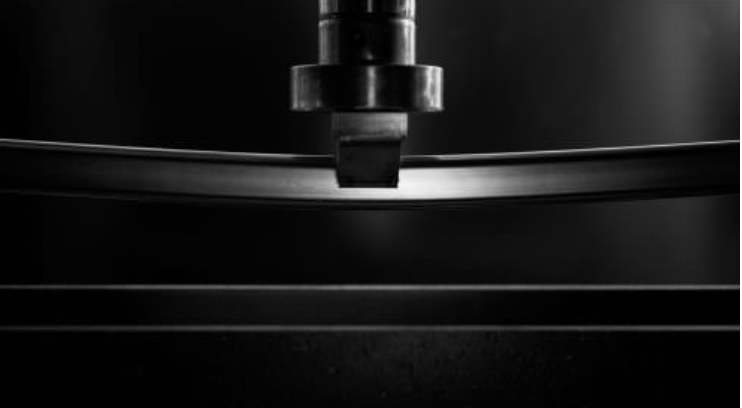
Proving the strength of formed tubes using mechanical bend tests
An exploration into two independent axial load tests on our stainless steel formed profiles, plus a brief look at how we calculate the degree of bends for formed tubes.
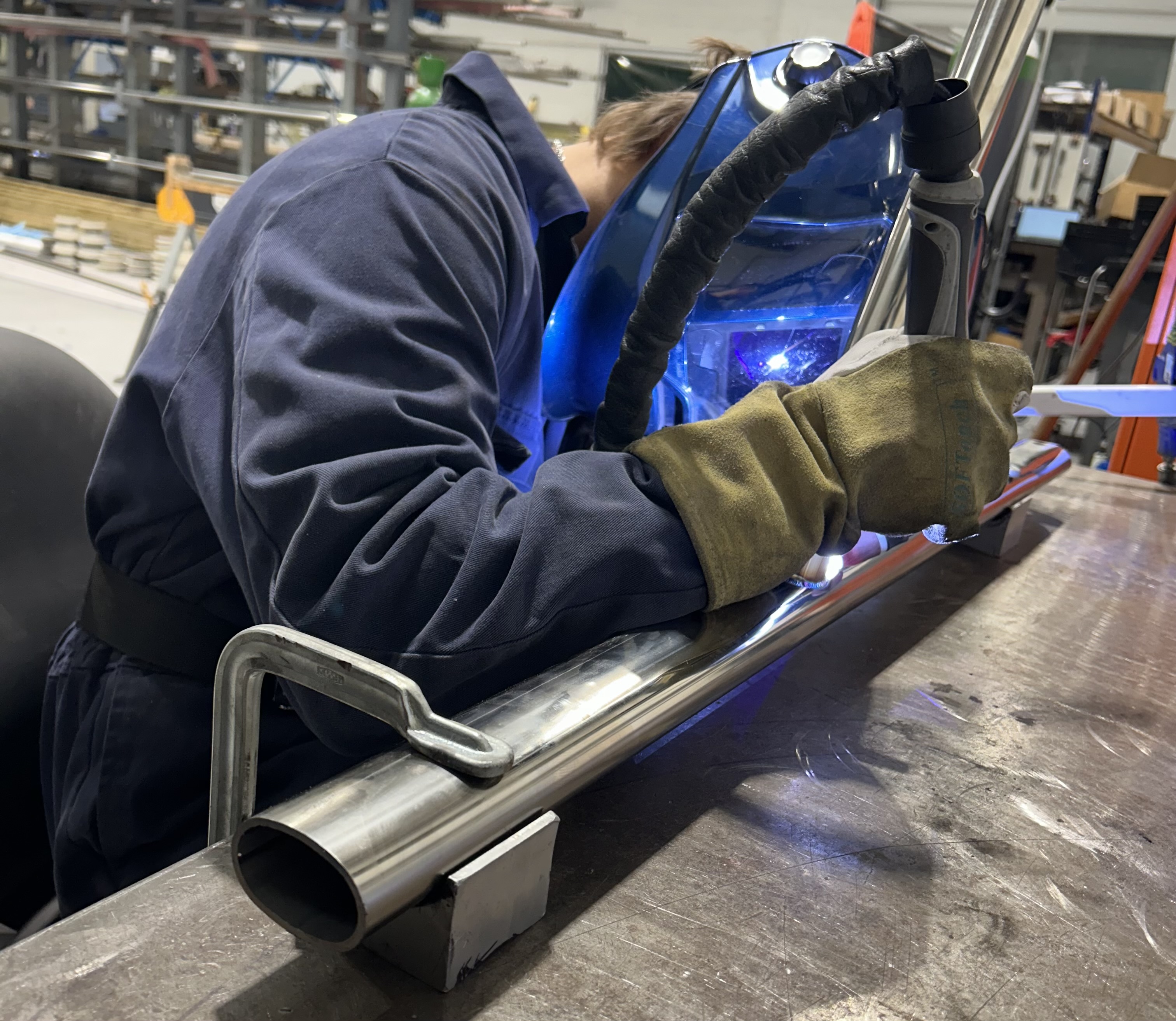
Exhibitors Timeless Tube engineer tube-based showcase for Southern Manufacturing and Electronics trade fair
Visitors to leading trade show for engineers and manufacturers to experience a showcase of innovative tube designs
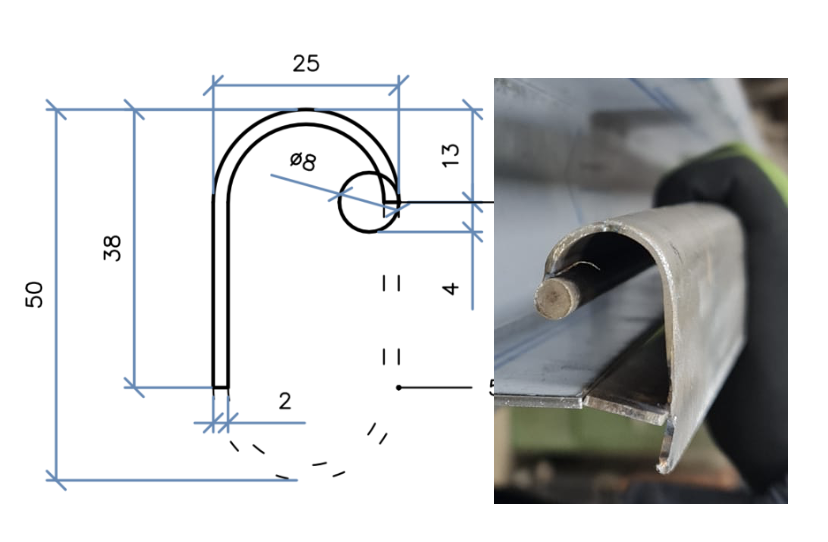
Cut Flat-sided Oval Tube Features in Stunning Recessed Handrail Project
Achieving unique designs often requires embracing trial and error. Timeless had the pleasure of working with pioneering UK-based bespoke steel fabricators Metcalfe on a one-of-a-kind recessed handrail