Premium grade metals and high quality finishes
Specify your tubes from our wide selection of materials and finishes
Below is an outline of the different metals available for tube fabrication, as well as the various finishes that we provide for our stainless steel tubing, brass tubing and aluminium tubing. If you have any questions on materials and finishes, our technical advisors can help guide you through the options available for your application.
Stainless Steel
Most of our tubing is fabricated from stainless steel because it is versatile, durable and sustainable. It is easy to clean, which makes it a hygienic choice for public buildings and healthcare applications.
Stainless steels are iron alloys with a minimum of 10.5% chromium. Other alloying elements such as nickel, molybdenum and titanium are added to enhance structure, formability and strength, as well as non-metals such as carbon and nitrogen. Stainless steel covers a wide range of steel types and grades for corrosion / oxidation-resistant applications; to qualify for each type or grade, it must meet the corrosion-resistance requirements.
We do not form our tubes from mild steel, or use any mild steel tooling, not only because it lacks the quality of stainless steel, but because it contaminates the stainless steel that we form from. The lack of alloying elements in mild steel means that it is prone to oxidisation (rust) if it’s not properly coated. By contrast, stainless steel boasts impressive anti-corrosive properties.
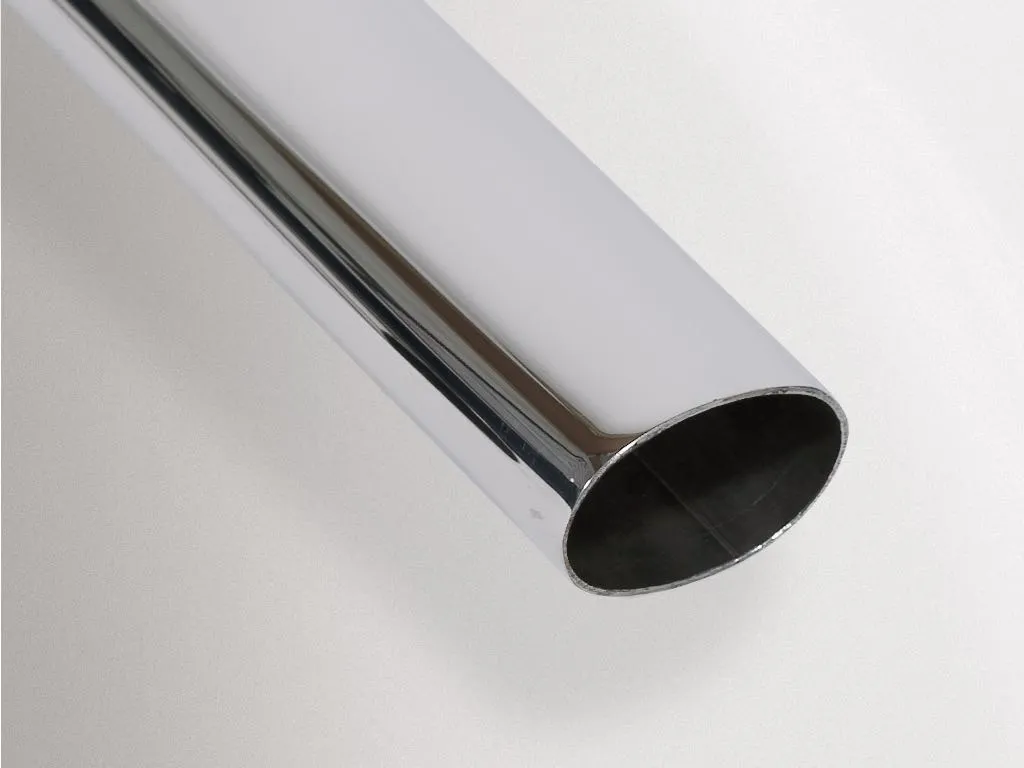
Stainless Steel Grades
Our Stainless Steel Finishes
Our specialist in-house polishing department provides a comprehensive choice of finishes for your metal tubing or components.
The team of talented polishers carefully hand polish metalwork using premium-grade mops and polishing compounds to ensure that you receive high quality results. We have a fastidious quality control procedure to make sure that all polishing work adheres to our Timeless standards.
A technical advisor can advise you on our Timeless polishing classification system, and what might be most suitable for your application. While the images below can be used as a guide, there is no substitute for having a physical sample of tubing or metalwork with your desired finish to allow you to make an informed choice.
Reflective finishes
These finishes are achieved using handheld oscillating machines, mops and compounds. There is no discernible grain to these finishes. This means that contaminants cannot reside in the grain, making these finishes a sensible choice for corrosive environments.
We typically polish tubing that is supplied with a mechanically produced commercial bright polish finish with a 600 grit.
This reflective finish has a better resistance to corrosion than a roughly polished surface. However it has a slightly grained texture, and is not free from all surface defects. We recommend that this finish is further polished when aesthetics are important to the application.
This finish is sometimes referred to a bright polish or bright buff.
Linear / Long Grain
Tubes with a commercial bright finish are polished once and buffed. Upon close inspection, it is possible to see the grain of the polishing running lengthways (longitudinally) in continuous lines along the tubing. This grit pattern is sometimes referred to as a hairline finish.
This offers greater reflectivity than commercial bright polish and is often chosen when aesthetics are important.
Circumferential Grain
Tubes with a commercial bright finish are polished once and buffed. Upon close inspection, it is possible to see the grain of the polishing running around the circumference of the tube.
This grit pattern (approx 800 grit) offers greater reflectivity than commercial bright polish.
Tubes with a commercial bright finish are linished, polished once then buffed twice.
There is no perceivable grain to this superior finish, as grit lines are removed through successive fine polishing processes.
This premium polish boasts an exceptional reflectivity. It sometimes referred to as super mirror polish or ultra mirror polish, but it is achieved using mops and compounds rather than wet chemicals.
Grained Finishes
These finishes are achieved using abrasive media.
Non-reflective and easy to maintain, these popular finishes can effectively disguise blemishes and fingerprints.
This fine-grain finish is the most refined from our range of grained finishes. While this finish has a perceivable direction of grain, this is smoother and more subtle than the brushed / grained finish.
To achieve this finish our polishers abrade a mirror polished tube /metal component using a coarse mop. It has an approximate grit of 320.
Satin polished tubing is supplied to Timeless with a uniform radial finish produced mechanically. This has an approximate grit of 320.
Please note that it is difficult to ‘touch up’ areas of this supplied satin polish post-fabrication by hand due to its uniform nature. If aesthetics are paramount, we recommend that a hand-polished satin finish is chosen instead.
Often referred to as sand-blasting, this process actually ‘blasts’ materials such as glass beads or even bicarbonate of soda onto metal to achieve a variety of grained finishes.
This is an attractive option if you require a textured but uniform finish. The finer the grain used (such as fine glass beads), the smoother and more delicate the finish.
This finish has deeper directional grain lines and is a coarser finish than the satin polish. It is created using a polishing belt rather than a mop. This finish has an approximate grit of 240.
This is sometimes referred to as a dull grit finish or dull polish. This is recommended for tubing and metal components post-fabrication.
Created using machines, tubes with a dull polish are typically supplied with an approximate grit of 240.
Other Finishes
If appearance is not important, or if finishing is to take place after further fabrication, we can also provide tubes with a mill finish or descaled finish.
Some clients choose to powder-coat tubes with a wood-effect powder finish or other colours.
Tubes can be colour-coated up to 3m long using PVD (Physical Vapour Deposition) titanium ion plating in a wide variety of colours – ideal if you require a specific colour or brass-effect but you need the tubing to be extremely tough. Unlike conventional methods of coating, PVD is significantly harder, making it scratch and corrosion resistant.
PVD is a colouring process only – it doesn’t change the finish on the substrate. The pre-colouring finish is exactly the same finish that you will see after the process, just with a different colour. This means that tubing and associated parts need to first have a finish applied to all the visible surfaces (brushed, mirror polished etc).
It is also important to note that with PVD coating, fabrication processes such as welding are likely to damage the finish. Please ask our fabrication team about our custom-made mechanical joiners for instances where you want to dry join parts such as railings in order to avoid welding.
Enquire about the range of colours available for stainless steel tube profiles.
Aluminium
Aluminium is an important material because it is light, durable and functional. It is one of the lightest metals but it’s also strong and flexible. Its surface is covered in an extremely thin yet strong layer of oxide film, which makes It highly corrosion-resistant. It also resists heat damage and is a great electricity conductor. It doesn’t magnetise, and it forms alloys with most other metals.
We have formed and fabricated tubing for several applications using aluminium - from bimini sun shades on yachts to retail hanging rails.
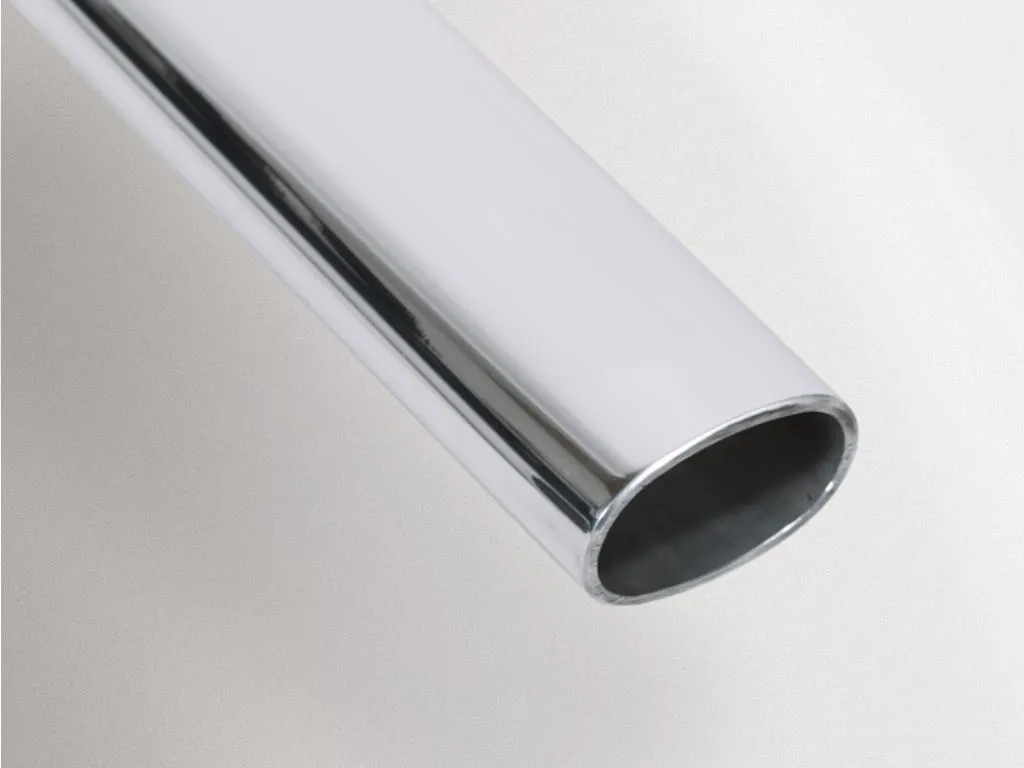
Aluminium Grades
Aluminium Finishes
We typically supply our custom-formed aluminium tubing with a mill finish. Upon request, we can apply a grained or sandblasted finish to aluminium if needed as a key for further powder-coating. It is advised that the metalwork is anodised after finishing to strengthen the metal and prevent it from oxidising.
This non-reflective finish is similar to the satin finish that we achieve in stainless steel. While this finish has a perceivable direction of grain, this is smoother and more subtle than the brushed / grained finish. To achieve this our polishers abrade a mirror polished aluminium tube or component using a coarse mop.
We strongly advise that the tubing and metal parts are anodised post-polishing to prevent the aluminium from oxidising. This will also serve to strengthen this relatively soft metal.
We work with trusted suppliers who can powder-coat pre-treated aluminium tubing to an excellent standard, helping to improve the metal's corrosion resistance and aesthetic appeal.
Powder coating is available in a wide range of colours and finishes.
If you want to achieve a reflective surface then we can polish the aluminium to a mirror finish.
We highly recommend that the tubing is anodised post-polishing. However please note that this thickened layer will slightly dull the metal’s brightness, so you may wish to get samples made prior to full production.
Our brushed / grained finish is similar to the brushed finish that we achieve in stainless steel. This finish has deeper directional grain lines than satin polish, and is a coarser finish than the satin polish. It is sometimes referred to as a dull polish.
We strongly advise that the tubing and metal parts are anodised post-polishing to prevent the aluminium from oxidising. This will also serve to strengthen this relatively soft metal.
Often referred to as sand-blasting, this process actually ‘blasts’ materials such as glass beads or even bicarbonate of soda onto metal to achieve a variety of grained finishes. This is an attractive option if you require a textured but uniform finish.
The finer the grain used (such as fine glass beads), the smoother and more delicate the finish.
Blasting also has the added benefit of preparing the surface for anodising by creating a better ‘key’ for the coating to bond to thanks to the tiny peaks and troughs that it forms on the substrate. The metal will need to be anodised after this process to prevent oxidisation.
If you have specified aluminium tubing for your application then you will probably find that you want to increase its robustness and resistance to corrosion by choosing to have it anodised. This electrolytic treatment produces a coating of aluminium oxide, which upon request, can be dyed to produce colours such as black, red, blue and purple.
We work closely with one of the UK’s leading aluminium anodisers to ensure that you get the right finish for your application. Typically our clients will select sulphuric anodising, which offers the same robustness as stainless steel (different thicknesses are available depending upon the desired hardness or colour).
For applications that require a thicker protective coating of over 25 microns, hard anodising will be required. It is important to note that a thick coat of anodising (such as hard clear anodising) is likely to darken the original shade of the base material. We urge all clients to consider this if aesthetics are crucial to the end-application.
Tubing and machined aluminium parts will need to be welded prior to anodising so as not to damage the surface.
Brass CZ108 H/H
Brass is an alloy consisting of copper and zinc, which is stronger than pure copper and provides a lighter, gold-like finish. Brass is the most common of the copper-based alloys. It has a good corrosion resistance. We typically use ‘basis brass’ for tube fabrication as it has excellent cold forming attributes, and can be readily soldered.
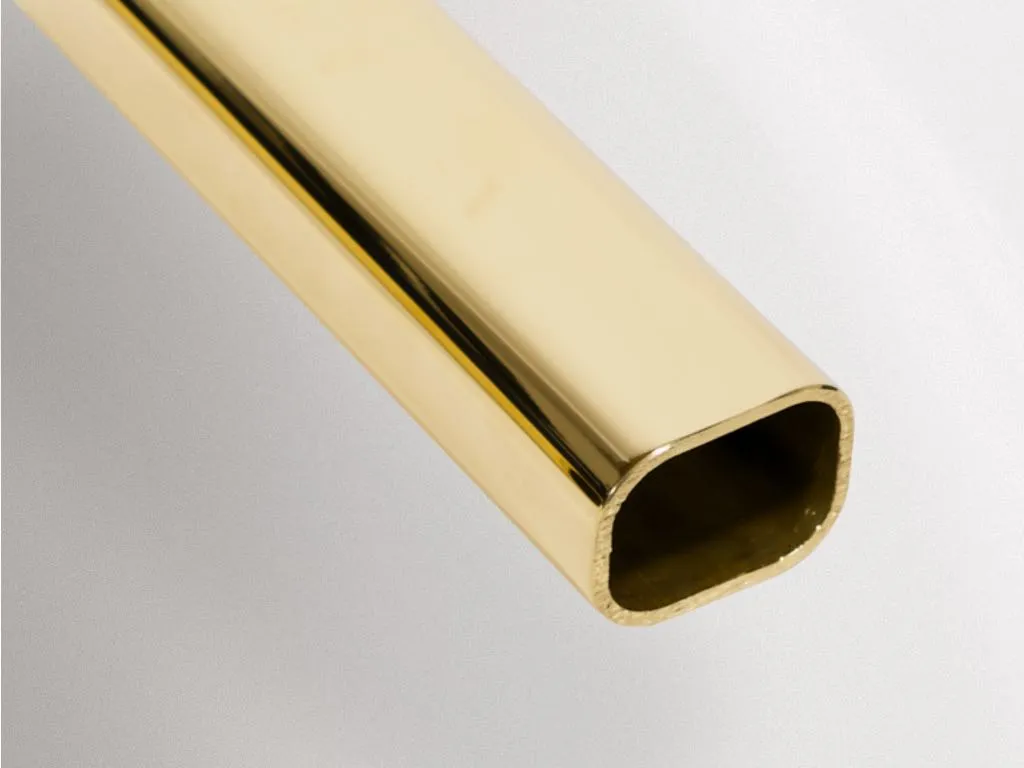
Brass Finishes
Our polishing team boast years’ of experience polishing brass tubing and components.
Brass is a soft material which allows for a variety of different polish finishes. Please also refer to the reflective polishes available for stainless steel, which can be achieved in brass.
Note that unlike stainless steel, brass may need to be waxed or lacquered after it has been polished to prevent oxidisation.
This non-reflective finish is similar to the satin finish that we achieve in stainless steel. While this finish has a perceivable direction of grain, this is smoother and more subtle than the brushed / grained finish. To achieve this our polishers abrade a mirror polished brass tube or component using a coarse mop.
We strongly advise that the tubing and metal parts are lacquered post-polishing to prevent the brass from oxidising.
If appearance is not important, or if finishing is to take place after further fabrication, we can also provide brass tubes with a mill finish.
This grained finish is similar to the dull finish that we achieve in stainless steel. This finish has deeper directional grain lines than satin polish. It is a coarser finish than the satin polish.
We advise that the tubing and metal parts are lacquered or waxed post-polishing if you want to prevent the brass from oxidising.
Lacquering is recommended for all brass work if you want to protect the brass from oxidisation. After degreasing, the brass is lacquered within environmentally controlled spray booths – sometimes over 2 or 3 individual paint sessions.
A spray application of specialist metal adhesion primer is applied, followed by coats of high-quality industrial grade 2 component polyurethane lacquer. This protective process will thicken the substrate (75-100 microns) so you may notice a slight reduction in the brightness from the polished tubing.
Cupronickel 90/10 CU90NI10
Also known as copper-nickel, cupronickel is a group of alloys containing copper and nickel. We use cupronickel 90/10, which contains 90% copper and 10% nickel, with small quantities of iron and manganese for strength and corrosion-resistance. Cupronickel 90/10 has a warm colour that is similar to bronze, which makes it an extremely cost-effective alternative to bronze.
Cupronickel has high electrical resistivity.
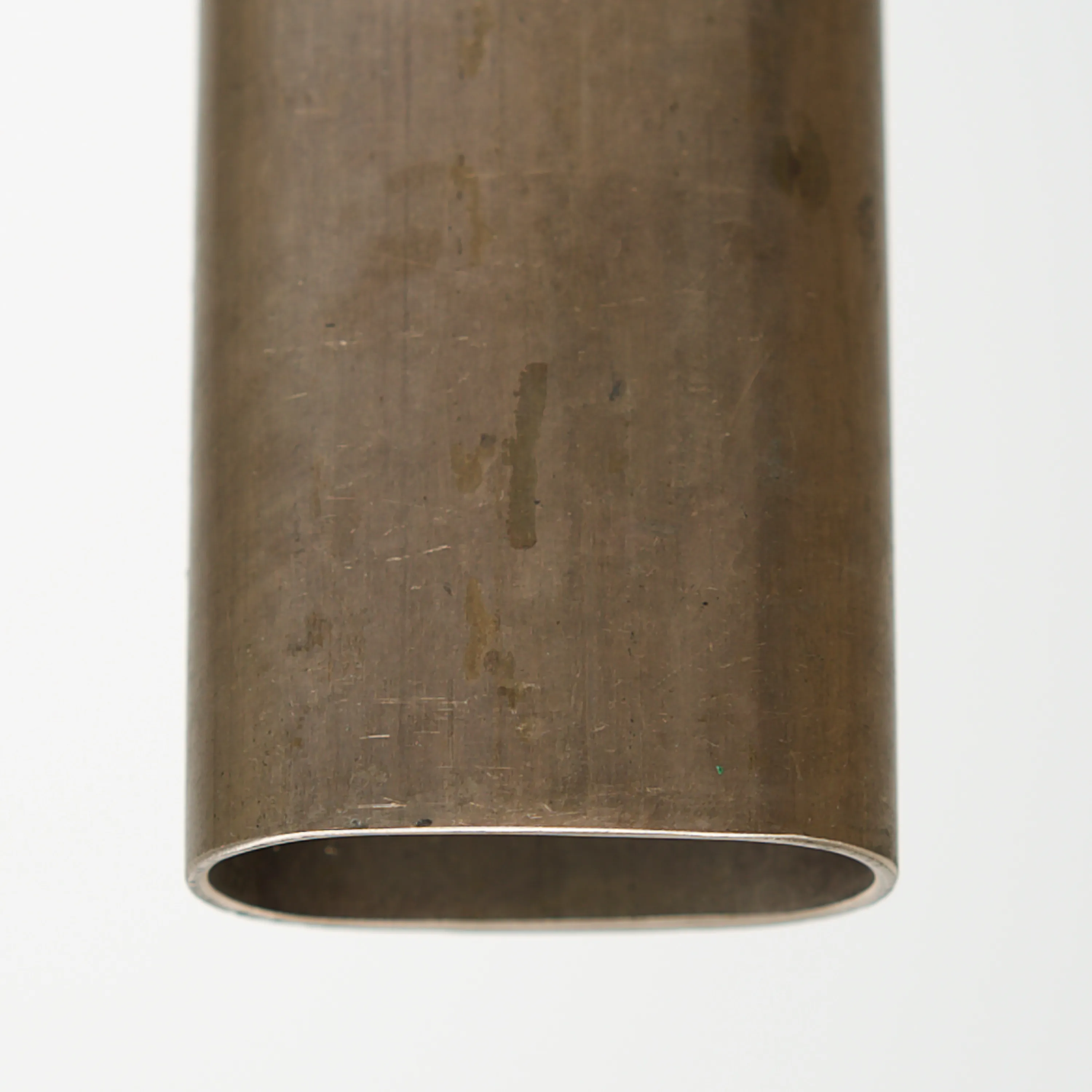
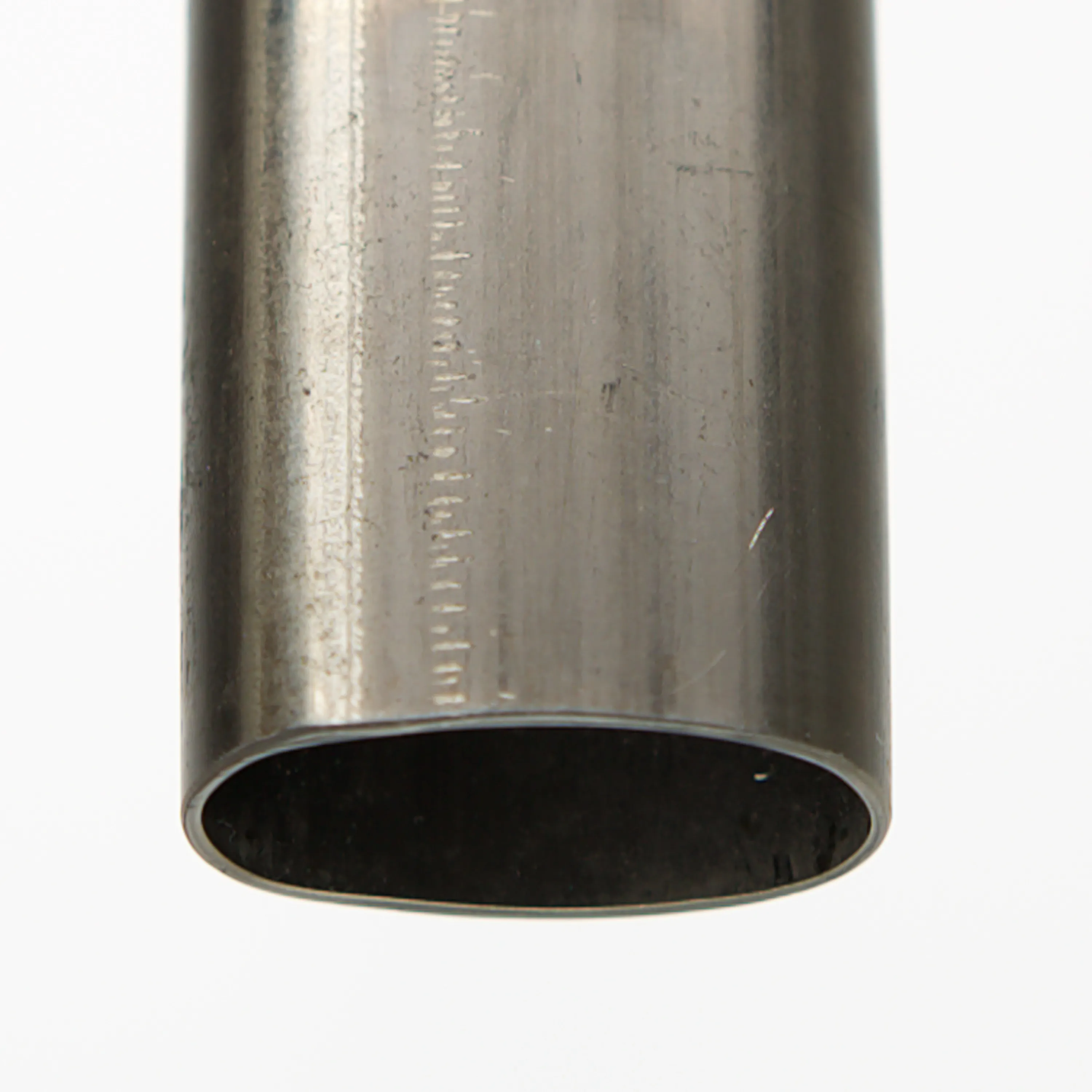
Other Metals
We can also form and fabricate custom-shaped tubing from other metals including titanium, copper and bronze — contact us for more information on using alternative materials.
Please note we do not use or polish mild steel in our workshops to prevent contamination issues.
Request a Sample
Our team will happily chat to you to help guide you through the options available for your application, and our Timeless polishing classification system.
While our images can be used as a guide, there is no substitute for having a physical sample of tubing or metalwork with your desired finish to allow you to make an informed choice. Please contact us to request samples.
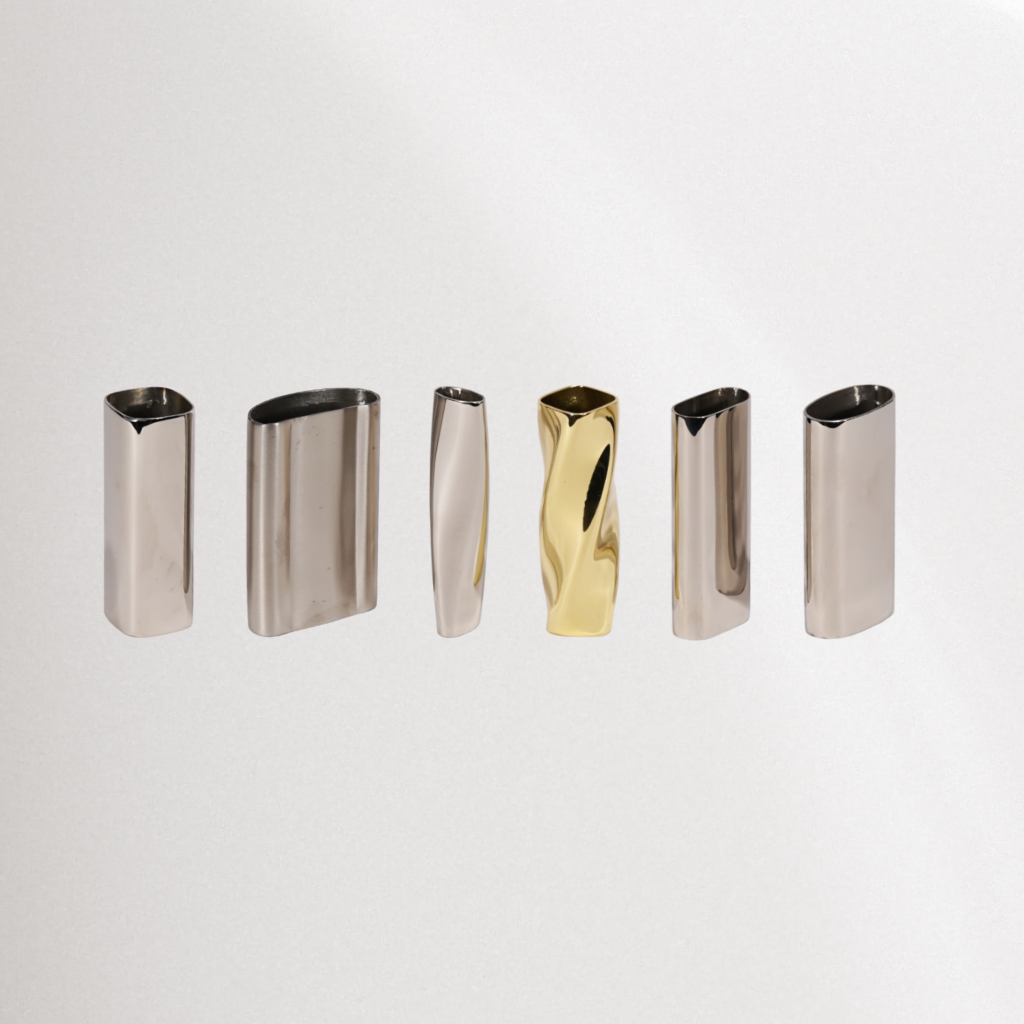