D-shaped tube enables 'game-changing' ground-movement monitors
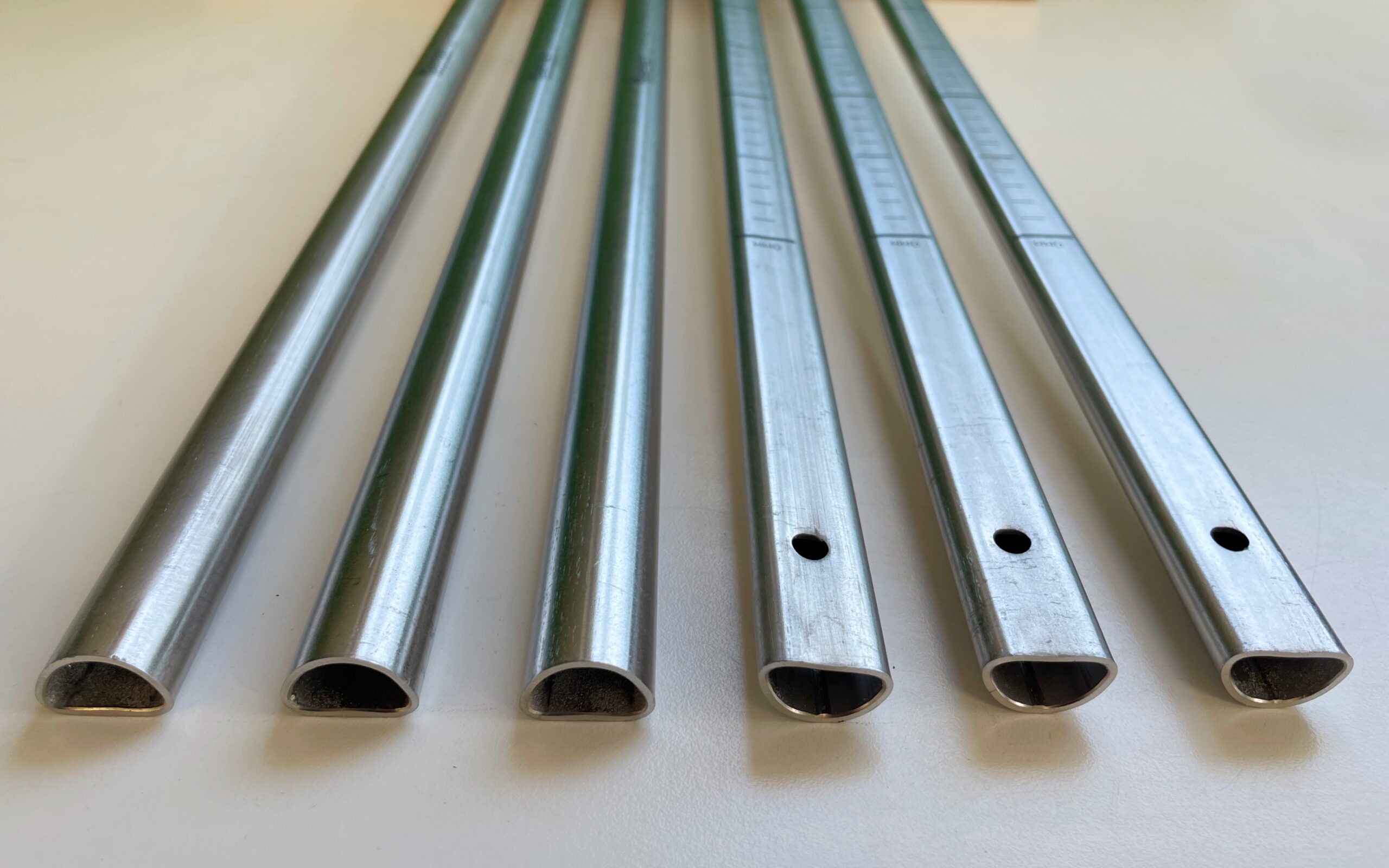
British engineers Osprey revolutionise construction surveying with automated geotechnical monitors made from Timeless stainless steel tubing
The smallest D-shaped tubing ever created by Timeless Tube has enabled the pioneering British engineering company Osprey Measurement Systems to create a ‘game-changing’ new device that makes the vital business of measuring soil displacement a more efficient, effective and safer process. The In-Place Extensometers (IPXs) are used for building embankments, excavations and tunnelling, and are already being widely used to monitor major infrastructure project HS2.
Timeless Tube was brought on at the latter stages of the development when tube engineers shaped the stainless steel tubing that provides robust IPX electronics. The engineers were required to build new tooling to make Timeless’s smallest D-shape tube to date, measuring 20×12.5×1.6mm.
A safer, more effective way to measure and maintain stable ground conditions
Before any construction or infrastructure work takes place, substantial resource is required to ensure the sites are stable and ready for construction. Soil is an unpredictable, complex material. When a large amount of soil is added or removed from a site, the ground is susceptible to compaction or expansion. The rate and magnitude of this compression or expansion is critical to maintaining stable ground conditions and protecting both the construction works and nearby infrastructure.
The automated IPXs, used with new or existing traditional magnetic probe extensometers, can remain in the ground for months or even years since they no longer need to be checked manually. Osprey’s Managing Director, Peter Scott, says: “Until now, magnetic extensometers haven’t been automated. Automation is about more than simply removing the cost of labour. It provides more reliable information, faster. It takes workers out of extremely high-risk areas, and allows monitoring to occur where access isn’t even an option.” continues Scott.
Near real-time measurements
The IPXs allow data to be received hourly, providing a superior dataset for better analysis in near real-time. Engineers are alerted by SMS or email as soon as an acceptable level of ground stability is reached and work can proceed, or when unexpected movement occurs so that immediate action can be taken. This makes for a more responsive construction process and removes the need to send out technicians to take daily or weekly manual readings for months or, in many cases, years.
The single vertical columns not only provide more regular, consistent data than other extensometer systems, but richer data that allows engineers to make more dynamic observations and forecasts – especially relating to rate and acceleration of change or changing conditions caused by weather patterns or site activity.
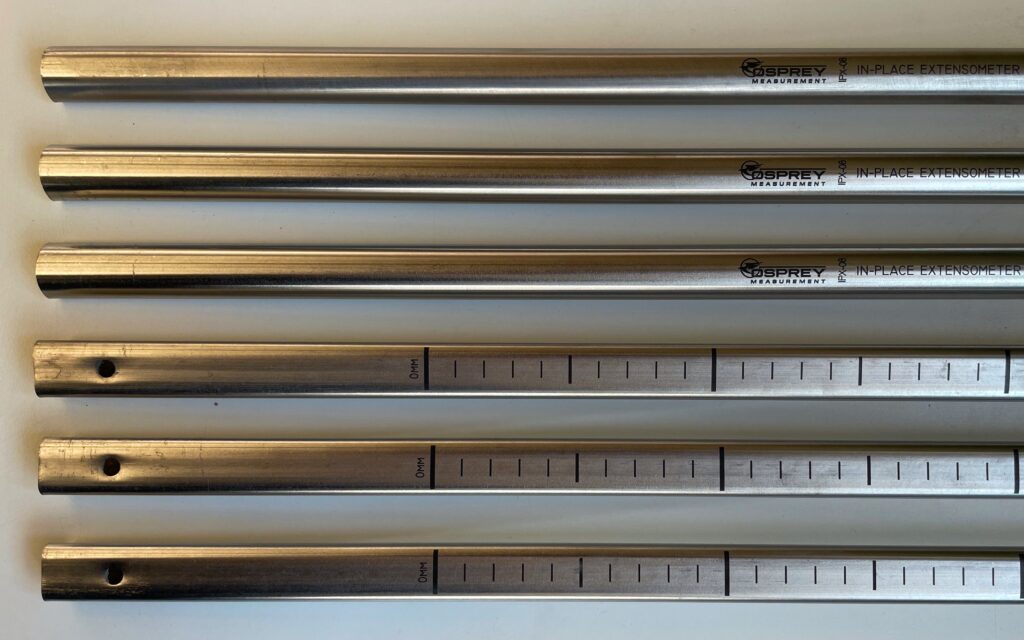
D-Shaped tubing – An enabling shape
The D-shaped tube enables a complete seal around the electronics inside, eliminating the threat of water ingress. The D-shaped design also minimises the space occupied by the IPX within the access tube, meaning a smoother installation.
Osprey’s Head Engineer Daniel Scott explains “The IPX needs to reliably operate in some very hostile subterranean environments, at significant pressures, and in the presence of corrosive groundwaters. After a lot of research and testing, we found advanced polymers and carbon fibre composites just not up to the task. It became clear that stainless steel was the right material. We spent some time looking at standard tube shapes and sizes but couldn’t find anything that met our specific needs. We contacted Timeless Tube with a fairly open request for a solution and a list of our requirements and constraints, including the very specific diameter dictated by the size of the access tube used. Their engineers proposed forming a D-shaped tube — a perfect fit for what we wanted. Further testing and refinement resulted in the solution meeting not just our mechanical requirements (dimensional consistency, rigidity and crush resistance), but also the necessity for the steel to be magnetically permeable.”
The printed circuit board fits snuggly into the unique D-Shaped tubing
But achieving this D-shaped tube was an engineering feat in itself, according to Timeless Tube MD and Head Engineer Tom McMillan “We are proud that our shaped tube has provided a solution for this significant new product. Creating a shape that successfully accommodates the sensors has been a challenge. Forming the unique profile required us to make new tooling: although we have made D-shaped tubes for other applications, the dimensions have never needed to be so small or with such critical tolerances. Made from marine-grade 316L stainless steel, the tubular casing has excellent rigidity and is capable of withstanding harsh working environments.”
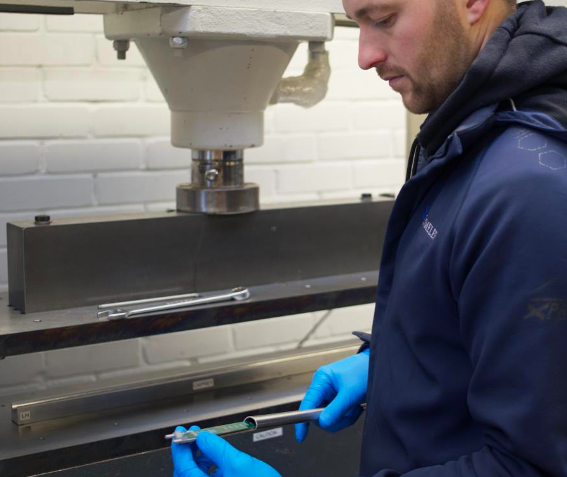
Osprey’s Daniel Scott adds, “The ability to work closely with Timeless on the tube prototype was vital. Having a UK-based manufacturer flexible enough to experiment with tooling and materials allowed us to get this product to market a lot quicker.
Many of the larger overseas manufacturers would not have the agility or set-up to make such modifications”.
How do the IPX sensors work?
The IPX is installed inside a small diameter access tube in a borehole, so space is very limited. The instrument is mounted onto a fibreglass rod to secure its position vertically. The D-shaped tube safely houses the electronics while allowing space for the fibreglass rod to run alongside the unit. Clamps on the top and bottom of the D- shape tubing fix the IPX to the fibreglass rod.
This design allows the IPX to be ‘side-loaded’ onto the fibreglass rod, simplifying the installation process and allowing on-site adaptability. Engineers can easily adjust sensor spacing according to site conditions, accommodating unexpected ground conditions.
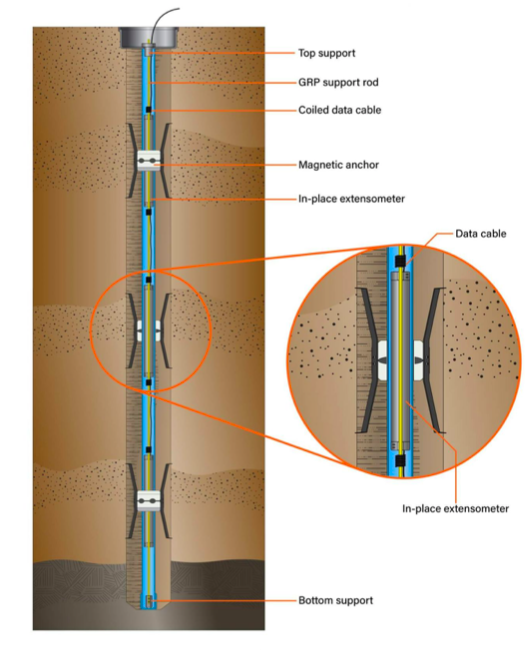
Founded by brothers Daniel and Peter Scott, Osprey Measurement Systems have developed this cutting-edge instrumentation in conjunction with University College London’s Department of Civil, Environmental and Geomatic Engineering, where Head Engineer Daniel Scott is also a lecturer in Reality Capture. It has taken several years to develop the IPX, which was built with additional support from leading geotechnical instrumentation specialists SOCOTEC Monitoring Systems, and in collaboration with British engineers Timeless Tube and a UK-based electronics supply chain.
Find out more about Osprey Measuring Systems.
The D-shaped tube is most typically used for handrail – find out more about this unique profile.
More stories
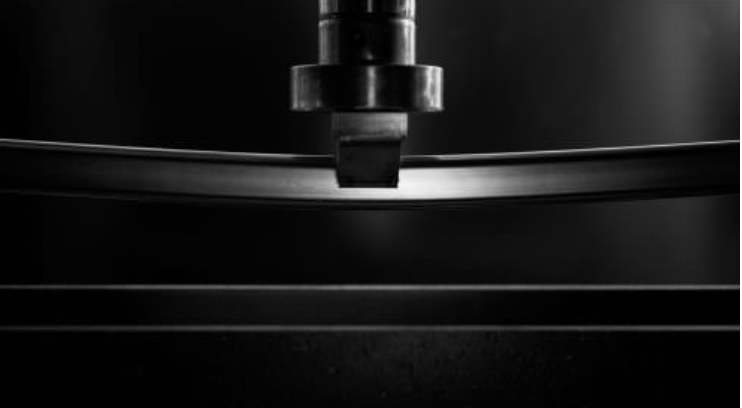
Proving the strength of formed tubes using mechanical bend tests
An exploration into two independent axial load tests on our stainless steel formed profiles, plus a brief look at how we calculate the degree of bends for formed tubes.
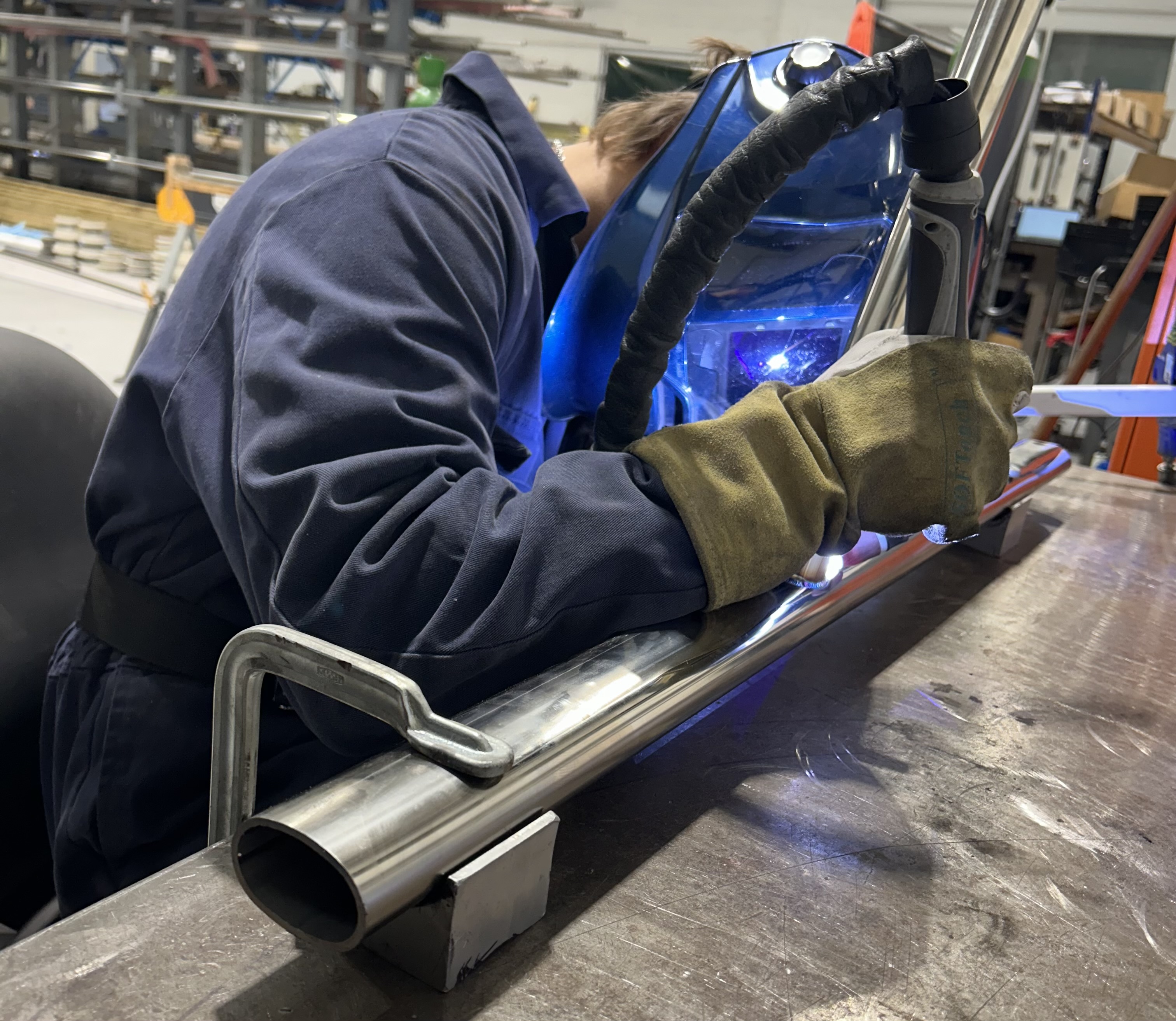
Exhibitors Timeless Tube engineer tube-based showcase for Southern Manufacturing and Electronics trade fair
Visitors to leading trade show for engineers and manufacturers to experience a showcase of innovative tube designs
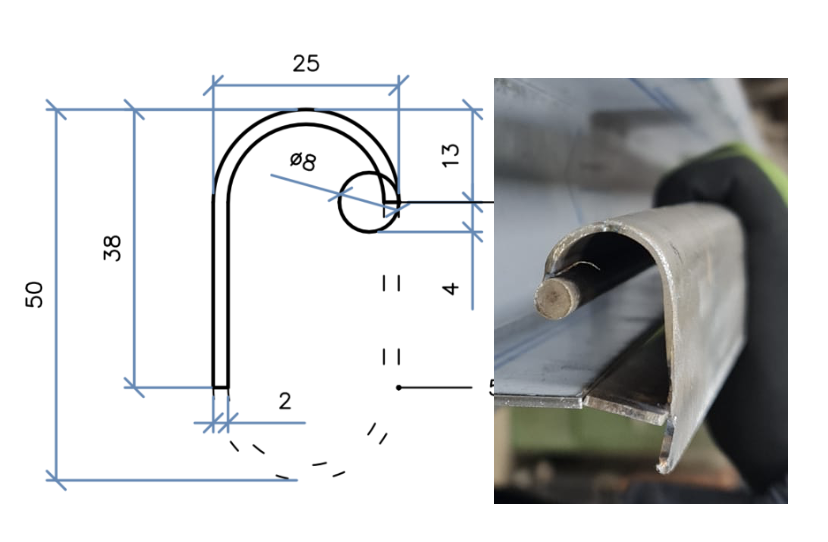
Cut Flat-sided Oval Tube Features in Stunning Recessed Handrail Project
Achieving unique designs often requires embracing trial and error. Timeless had the pleasure of working with pioneering UK-based bespoke steel fabricators Metcalfe on a one-of-a-kind recessed handrail